Datasheet Linear Technology LTM4676
Manufacturer | Linear Technology |
Series | LTM4676 |
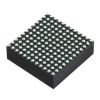
Dual 13A or Single 26A µModule (Power Module) Regulator with Digital Power System Management
Datasheets
LTM4676: Dual 13A or Single 26A μModule (Power Module) Regulator with Digital Power System Management Data Sheet
PDF, 2.2 Mb, File uploaded: Sep 25, 2017
Extract from the document
Packaging
LTM4676EY#PBF | LTM4676EY#PBF-ES | LTM4676IY | LTM4676IY#PBF | |
---|---|---|---|---|
N | 1 | 2 | 3 | 4 |
Package | 16mm x 16mm x 5.01mm BGA Package Outline Drawing | |||
Package Code | BGA | |||
Package Index | 05-08-1920 | |||
Pin Count | 144 |
Parametrics
Parameters / Models | LTM4676EY#PBF![]() | LTM4676EY#PBF-ES | LTM4676IY![]() | LTM4676IY#PBF![]() |
---|---|---|---|---|
ADC | 16-Bit | |||
DAC | 12-Bit | |||
Demo Boards | DC2087A,DC1811B-KIT,DC2269A-A | |||
Design Tools | LTpowerPlay ,LTspice File,LTpowerCAD File,Linduino File | |||
Export Control | no | |||
Features | Burst Mode, Differential Remote Sense, PolyPhase, PMBus, I2C Control, Watchdog Timer, EEPROM, ADC, DCR Current Sense, Sequencing, Margining, Tracking, External Synchronization | |||
Function | DC/DC uModule Regulator With Power System Management | |||
I/O | PMBus/SMBus/I2C | |||
Isupply, mA | 15 | |||
Monitors | Vin, Iin, Vout, Iout, Temperature and Faults | |||
Number of Outputs | 2 | |||
Operating Temperature Range, °C | 0 to 85 | |||
Supply Voltage Range | 4.5V to 26.5V | |||
Vin Max, V | 26.5 | |||
Vin Min, V | 4.5 |
Eco Plan
LTM4676EY#PBF | LTM4676EY#PBF-ES | LTM4676IY | LTM4676IY#PBF | |
---|---|---|---|---|
RoHS | Compliant |
Application Notes
- Accurate Temperature Sensing with an External P-N Junction &mdash AN137PDF, 540 Kb, File published: Sep 20, 2012
Many Linear Technology devices use an external PNP transistor to sense temperature. Common examples are LTC3880, LTC3883 and LTC2974. Accurate temperature sensing depends on proper PNP selection, layout, and device configuration. This application note reviews the theory of temperature sensing and gives practical advice on implementation.Extract from the document - Overview of the EEPROM in LTC PSM Devices &mdash AN145PDF, 3.0 Mb, File published: May 10, 2014Extract from the document
- Power System Management Addressing &mdash AN152PDF, 169 Kb, File published: Jul 12, 2016Extract from the document
- Linduino for Power System Management &mdash AN153PDF, 1.3 Mb, File published: Feb 24, 2016Extract from the document
- Fault Log Decoding with Linduino PSM &mdash AN155PDF, 230 Kb, File published: Jan 26, 2017Extract from the document
- In Flight Update with Linduino &mdash AN166PDF, 1.1 Mb, File published: Apr 10, 2017Extract from the document
Design Notes
- Dual 13A ОјModule Regulator with Digital Interface for Remote Monitoring & Control of Power &mdash DN524PDF, 337 Kb, File published: Jan 14, 2014Extract from the document
Articles
- Avoid Debugging Cycles in Power Management for FPGA, GPU and ASIC Systems &mdash LT JournalPDF, 3.2 Mb, File published: Aug 25, 2016Extract from the document
Model Line
Series: LTM4676 (4)
Manufacturer's Classification
- µModule Solutions > µModule Regulators > µModule Buck Regulators
- Monitor, Control and Protection > Digital Power System Management > DC/DC uModule With Power System Management
- Power Management > Switching Regulator > Step-Down (Buck) Regulators > Multiple Output Buck
- Power Management > Switching Regulator > Digitally Programmable Regulators