Datasheet TMC2590 (TRINAMIC) - 9
Manufacturer | TRINAMIC |
Description | Power Driver for Stepper Motors |
Pages / Page | 64 / 9 — 3.1 Standard Application circuit. +VM. Figure 2 Standard application … |
File Format / Size | PDF / 2.0 Mb |
Document Language | English |
3.1 Standard Application circuit. +VM. Figure 2 Standard application circuit
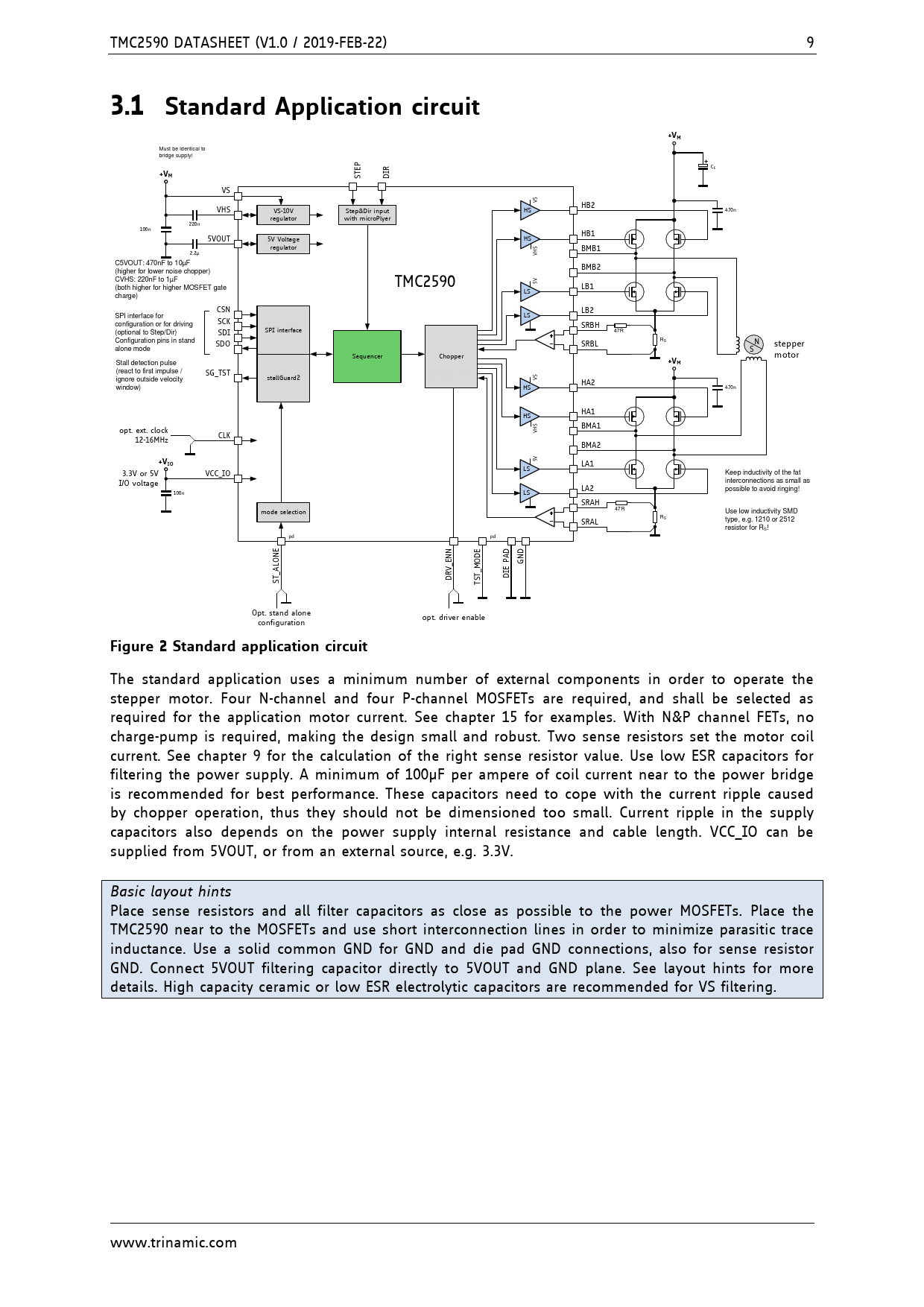
Model Line for this Datasheet
Text Version of Document
link to page 51 link to page 35 TMC2590 DATASHEET (V1.0 / 2019-FEB-22) 9
3.1 Standard Application circuit +VM
Must be identical to bridge supply! PE C T RI E
+VM
S D VS VS HB2 VHS VS-10V Step&Dir input HS 470n regulator with microPlyer 220n 100n HB1 5VOUT 5V Voltage HS regulator S BMB1 2.2µ HV C5VOUT: 470nF to 10µF BMB2 (higher for lower noise chopper) CVHS: 220nF to 1µF (both higher for higher MOSFET gate TMC2590 5V LB1 LS charge) CSN LB2 SPI interface for LS SCK configuration or for driving SRBH SPI interface 47R (optional to Step/Dir) SDI Configuration pins in stand SDO RS N SRBL stepper alone mode S Sequencer Chopper motor
+V
Stall detection pulse
M
(react to first impulse / SG_TST B.Dwersteg, © stallGuard2 TRINAMIC 2014 VS ignore outside velocity HA2 window) HS 470n HA1 HS S BMA1 opt. ext. clock H CLK V 12-16MHz BMA2
+V
5V
IO
LA1 LS 3.3V or 5V VCC_IO Keep inductivity of the fat I/O voltage interconnections as smal as LA2 possible to avoid ringing! 100n LS SRAH mode selection 47R Use low inductivity SMD RS type, e.g. 1210 or 2512 SRAL resistor for RS! pd pd E N E D NE AD N _ OD G P ALON V M E _ R _ I T D TS D S T Opt. stand alone opt. driver enable configuration
Figure 2 Standard application circuit
The standard application uses a minimum number of external components in order to operate the stepper motor. Four N-channel and four P-channel MOSFETs are required, and shall be selected as required for the application motor current. See chapter 15 for examples. With N&P channel FETs, no charge-pump is required, making the design small and robust. Two sense resistors set the motor coil current. See chapter 9 for the calculation of the right sense resistor value. Use low ESR capacitors for filtering the power supply. A minimum of 100µF per ampere of coil current near to the power bridge is recommended for best performance. These capacitors need to cope with the current ripple caused by chopper operation, thus they should not be dimensioned too small. Current ripple in the supply capacitors also depends on the power supply internal resistance and cable length. VCC_IO can be supplied from 5VOUT, or from an external source, e.g. 3.3V. Basic layout hints Place sense resistors and all filter capacitors as close as possible to the power MOSFETs. Place the TMC2590 near to the MOSFETs and use short interconnection lines in order to minimize parasitic trace inductance. Use a solid common GND for GND and die pad GND connections, also for sense resistor GND. Connect 5VOUT filtering capacitor directly to 5VOUT and GND plane. See layout hints for more details. High capacity ceramic or low ESR electrolytic capacitors are recommended for VS filtering. www.trinamic.com